Spare Parts Management Solution for new Logistics Centre
17th September 2024
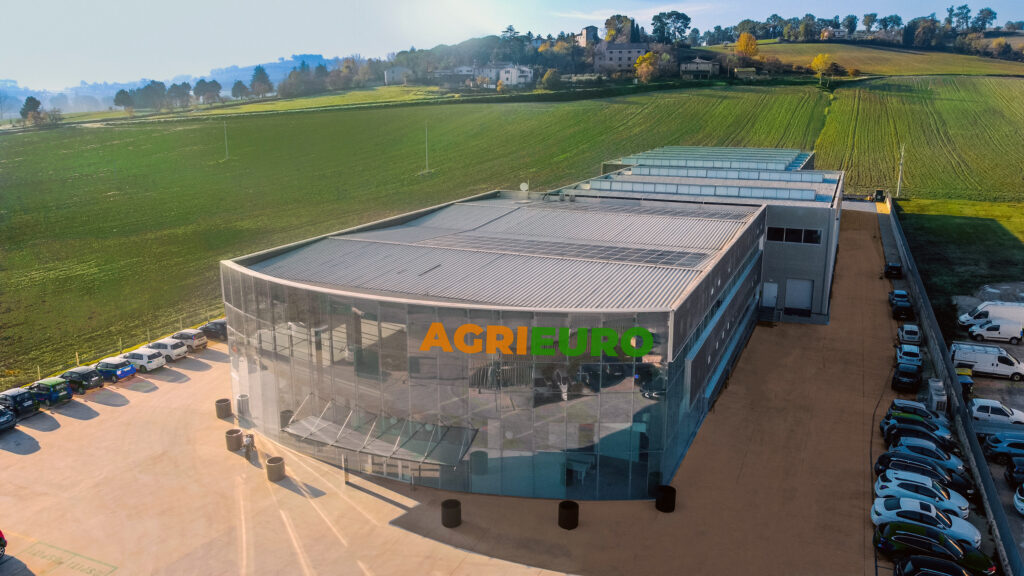
AgriEuro, a leading supplier of agricultural and garden equipment, recently selected Dematic to install an AutoStore system at its new logistics centre in Spoleto. The facility is scheduled to be built in the coming months and expands the site, which is currently the location of the company headquarters. It is set to focus exclusively on after-sales activities such as the management of spare parts and other small components.
“We were asked to design a scalable, automated solution that can meet current storage and performance needs and be easily expandable to support future growth, raises the level of comfort and safety AgiEuro’s warehouse operators and meets environmental and financial sustainability goals,” notes Rosario Filomena, a sales manager at Dematic.
According to Filomena, the decision to use the AutoStore system allows Dematic to ensure that every customer requirement could be met; along with the design of ‘swing-door’ component, which further optimises the warehouse space and helps to make the overall solution even more sustainable by significantly reducing the floor area in the new building. Additionally, the system’s low energy consumption directly responds to environmental measures the company wanted to see realized. “It completes a fantastic picture which makes it the best response to meet the green challenges of the future,” concludes Filomena.
Thanks to a unique design by Dematic, the AutoStore system enables AgriEuro to make optimal use of space by stacking boxes on top of one another and by storing numerous references within a single box. The system also automatically ‘learns’ over time which products have a higher rotation, positioning the relevant crates at the top of the grid to accelerate processing times. Filomena says it is a fully scalable solution which is perfectly suited to AgriEuro’s needs.
Spare Parts Management Solution
The AutoStore system to be implemented by Dematic calls for the use of 32,000 totes for a total storage capacity of more than 2,000 cubic meters of products. On the surface of the grid, 12 robots are positioned to achieve a handling capacity of 240 movements per hour with five material entry and exit doors operated by AgriEuro staff. The AutoStore solution is based on a “goods to person” process which eliminates the need for order picking and offers an ergonomically-improved work environment for warehouse staff.
AgriEuro’s decision to opt for a solution involving AutoStore to manage replacement processes actually goes beyond the simple need to optimise space utilization; it represents a strategic investment emphasizing after-sales service as a distinctive brand element in the market.
“It renews a centralized approach for our after-sales service management by boosting storage capacity to more than 1,000,000 spare parts for 40,000 machine models. We anticipate jumps when it comes to our customer service levels with respect to accuracy and timing in the shipment of spare parts, as well as the speed in their servicing,” says Roberto Arduini, a logistics manager of AgriEuro.
“The introduction of the AutoStore system is part of a broader investment framework within the construction of our new logistics area here at our headquarters,” explains Filippo Settimi, the CEO at AgriEuro, adding, “We are strongly committed to the growth of our employees and our organization in general and we are confident that the AutoStore solution offers us perspectives and opportunities for the development of new processes that can always help to further improve our service offer.”
similar news